- 800-277-7007
- ISO 9001:2015 Certified Company
Types of Plastic Materials and Additives
Plastic products are found in just about every home and business across the globe, so it’s important to understand the types of materials and additives that make them. Many consumers don’t realize that not all plastics are created equal, as there are a wide variety of manufacturing processes that produce a myriad of poly materials. Knowing the distinctions between these products helps you as a manufacturer, shipper, retailer, or buyer understand what will work best for your specific applications.
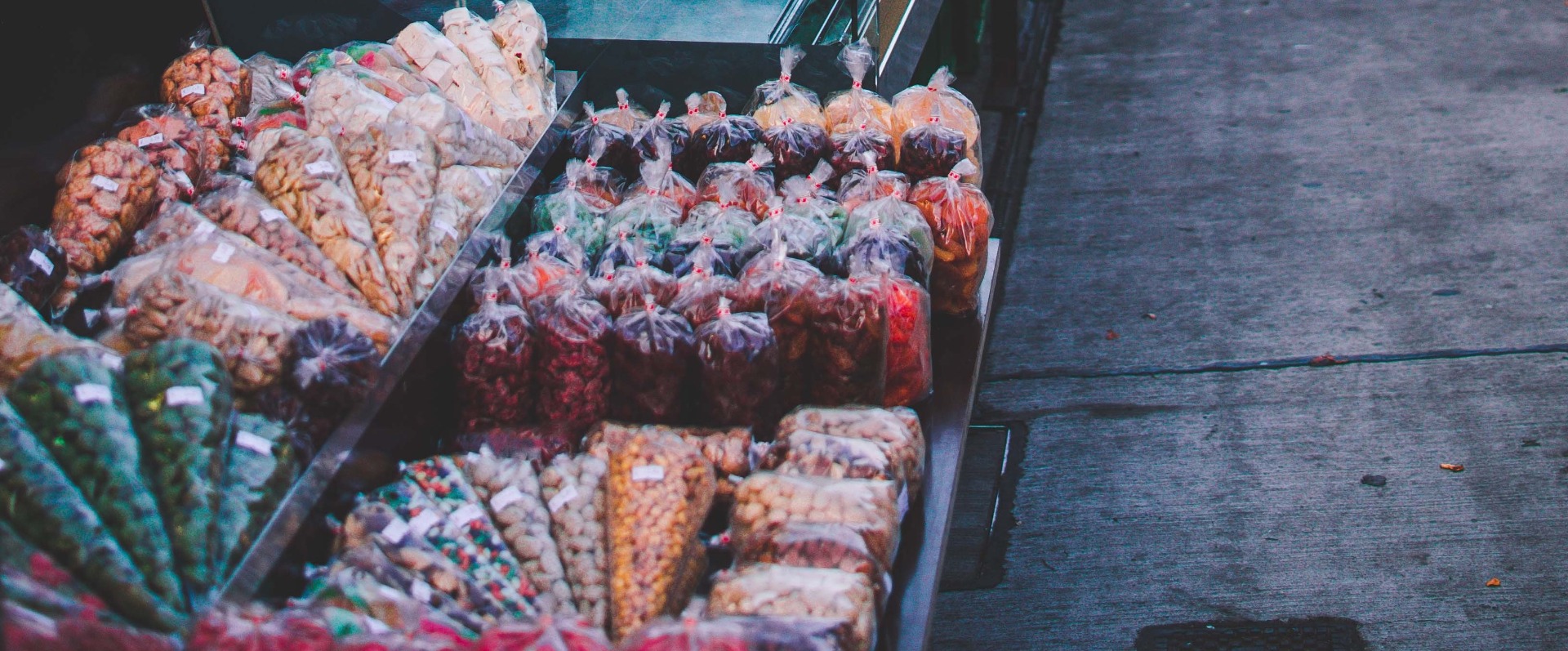
Standard Low-Density Poly Material
Low-density polyethylene (LDPE) is among the most versatile material for plastic packaging. It is used for a diverse range of products because of the many benefits it provides. LDPE offers incredibly high clarity to display goods beautifully, while also maintaining excellent protection to the items it holds or covers at the same time. For this reason, the majority of our poly bags and films are constructed from low-density polyethylene and the same is true for most low thickness materials like poly tubing, pallet covers, gusseted bags, and flat bags.
Linear Low-Density Plastic
Linear low-density polyethylene film, often referred to as LLDPE film, boasts a molecular configuration that makes it an ideal fit for situations where strength and puncture resistance are more important than high clarity. This is because it generally stretches more than standard low-density films do before breakage occurs. However, LLDPE films are usually lighter with lower barrier protection than their LDPE counterparts. Linear low-density resins allow bags or other goods to provide a thinner gauge that can be bottom sealed for premium strength. We offer many LLDPE bags that are a great option for food applications, as they meet FDA and USDA standards for food storage. Best of all, linear low-density polyethylene is almost always more affordable than LDPE material.
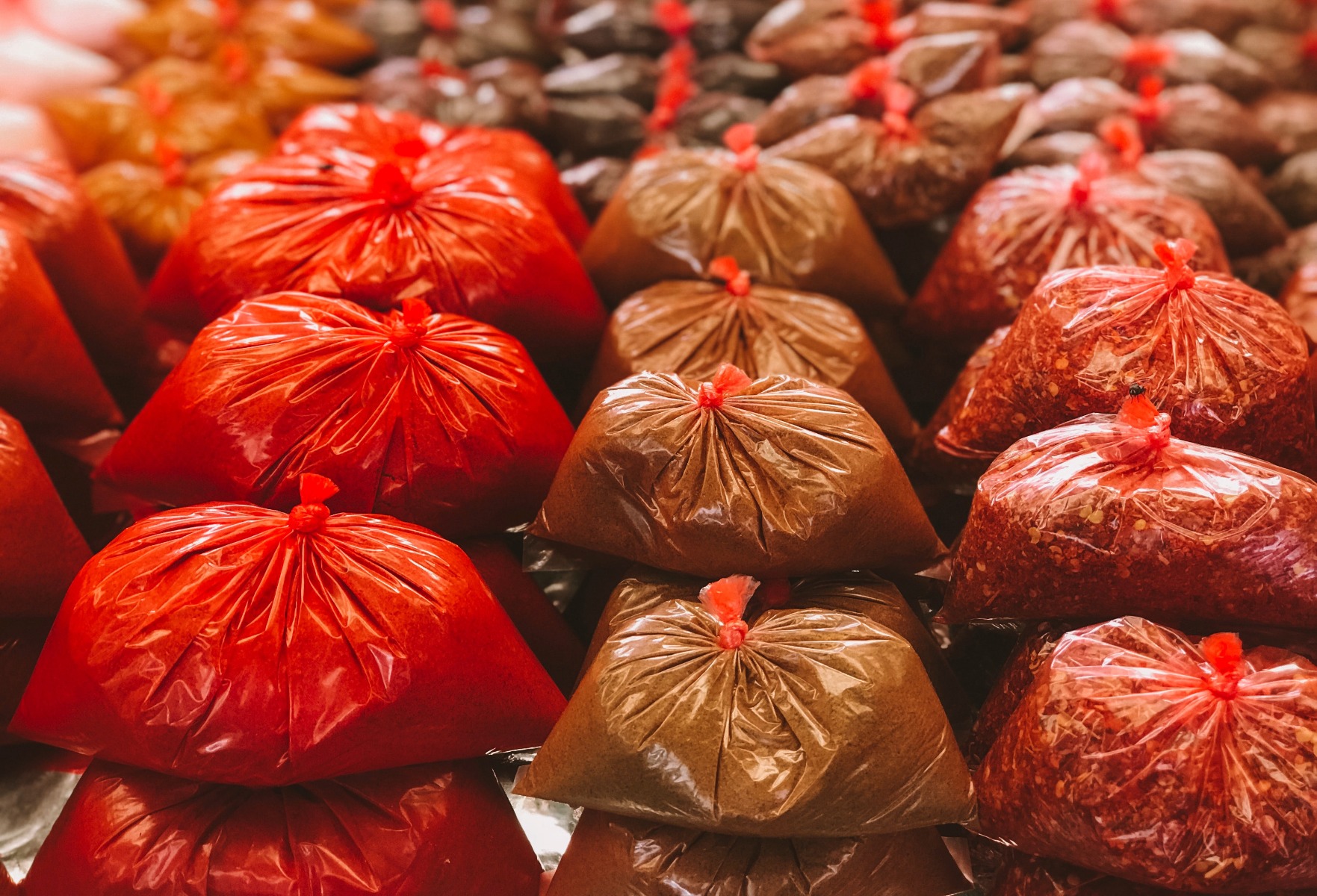
Transparent Material
Transparent plastic materials are simply defined as a film that you can see through and that light is easily able to pass through, no matter the color of the plastic. This means that transparent poly bags are the ideal choice for those who need customers to see the product inside its packaging. Transparent plastic is frequently used in the food industry, by small parts manufacturers, and for other applications where the customer may not be willing to purchase an item without seeing it first.
Opaque Plastic
Unlike their transparent counterparts, opaque materials do not allow customers to see through to the goods they cover. Because they block buyers from seeing what’s underneath, opaque poly bags are best for those who want extra protection for their products. Many conductive bags are an opaque black color that prevent shocks from harming the small electronics that are generally placed inside.
Ethyl-Vinyl Acetate
Ethyl-vinyl acetate (EVA) is an additive that’s used in polyethylene resin. When it composes about 2-3% of the material, it can enhance the bag’s or film’s strength considerably. Most often, we see EVA additives used in materials that will eventually be frozen, as it helps the film resist cracking.
Anti-Block
Polyethylene and other resins are often enhanced by anti-block additives that help the end user access the products inside the film or bag. This process takes place during extrusion, at which point the anti-block additive essentially bleeds into the poly material to make it easier to open the final bag.
Non-Scratch
On the opposite side of anti-block additives are non-scratch bags. These poly films contain minimal or no anti-block additives, as the anti-block material is often a very fine powder that can scratch the most delicate or sensitive products. Obviously this makes anti-block bags a poor choice for fragile items, but non-scratch prevents this problem from occurring. However, non-scratch plastic material is much more difficult to open.
Slip
Slip refers to a type of additive that can be mixed into polyethylene and other poly resins to improve their handling performance. It is added during the extrusion process, where the slip goes into the exterior of a plastic film and enhances the material’s ability to glide. This means that bags with slip additives are easy to handle and will not stick to one another when packaged into one larger container or box. Essentially, high-slip materials glide and slide against each other during the handling process, while low-slip materials prevent movement and provide easier grip.
Poly Bags for Everyone
Are you new to buying poly bags? Understanding exactly which poly bag is best for your products can be tough, so we hope this explainer was helpful. Let us assist you even further with a free poly bag conversion chart. It’ll help you determine what type of bag to use for certain products. All you need to do is fill out this form and we’ll email it to you right away!
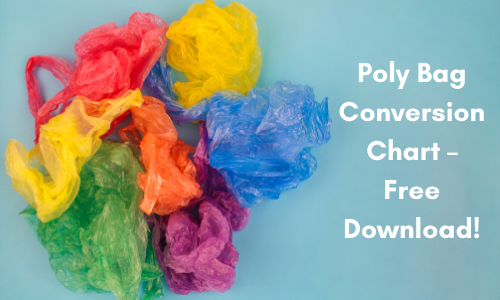